K2022. KraussMaffei отольёт ящик за 35 секунд, но из трёх "вторичек" сразу
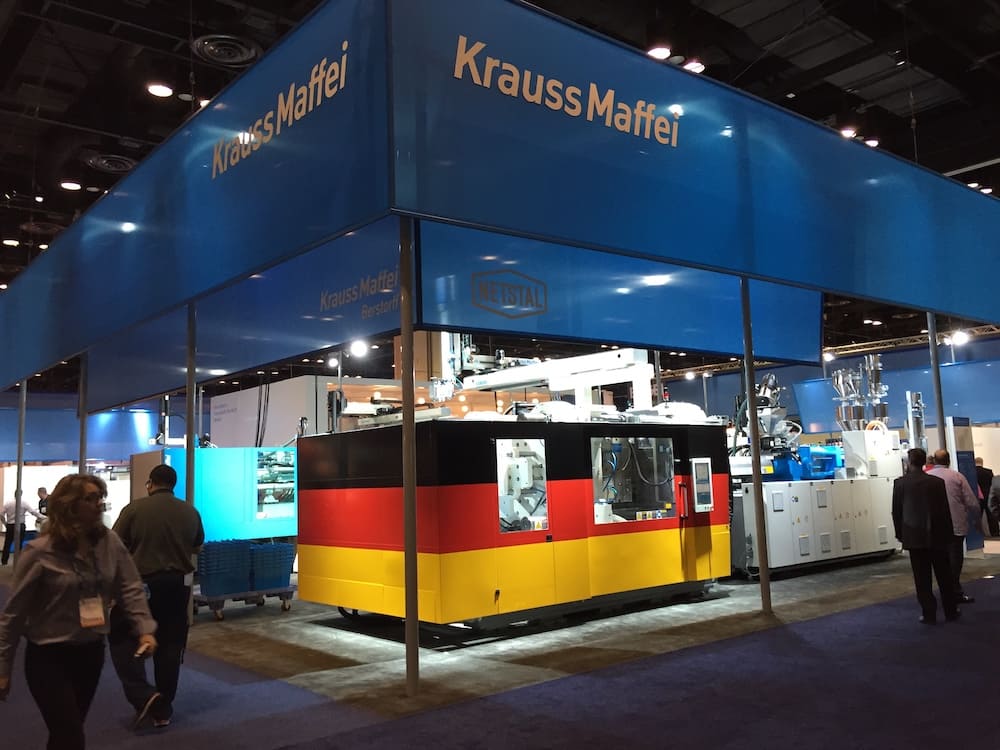
На стартующей 19 октября выставке К2022 в Дюссельдорфе компания KraussMaffei покажет как обеспечить совместное использование различных исходных вторичных материалов. Об этом предприятие из Германии сообщило сегодня ПластЭксперту. Такое оказалось возможно с помощью технологии DCIM (литье под давлением с прямым компаундированием) три различных вязких полимера превращаются в один новый продукт.
На стенде KraussMaffei будет демонстрироваться как три совершенно разных по реологии полимера можно переработать в ценное изделие. А именно дробленое полипропиленовое волокно из высокотекучего ПП из использованных масок FFP2 (объемная скорость расплава MVR=800-1000), измельченный ПЭВП (ПНД) из логистических ящиков (MVR=5-15) и отходы выдувного формования ПЭВП (ПНД) от производства игрушек (MVR<1). Эти исходные материалы различной вязкости будут смешены при использовании технологии DCIM для создания нового материала. В качестве добавок будут применяться мастербатчи, стабилизаторы и некоторые другие. На выставочном стенде KraussMaffei на К2022 полученный компаунд превращаются в складные ящики для транспортировки рыбы, состоящие из пяти компонентов. Время цикла литья такого непростого продукта составит 35 секунд.
Для успеха описанного процесса используется одношнековый экструдер DCIM, который экономически привлекателен уже при массе впрыска от 50 граммов и остается таким до впрыска в 2 кг. В то время как используемый ранее компанией двушнековый экструдер IMC требует как минимум 1500 граммов впрыска. Цель в обоих случаях одна и та же: смешать, модифицировать добавками, укрепить или наполнить полимеры и интегрировать это в процесс литья под давлением без потерь во время цикла.
Новый DCIM экструдер компактно устанавливается непосредственно над узлом впрыска стандартной гидравлической литьевой машины KraussMaffei (обычно серии GX, на стенде будет работать GX 1100-4300). Смешанный расплав подается в блок пластификации за один процесс нагрева, другими словами, без охлаждения или буферного хранения. Это существенно снижает деградацию полимера в цилиндрах. Кроме того, одноэтапный процесс экономит энергию и снижает выбросы углекислого газа. Экструдер и литьевая машина работают в прерывистом режиме, то есть при достижении объема впрыска для следующего цикла экструдер останавливает свою работу. Чтобы достичь этого идеально и превратить шесть отдельных компонентов в один однородный расплав, экструдер имеет специально разработанный шнек, с повышенным соотношением длины к диаметру. Для стандартных термопластавтоматов это отношение составляет около 17-23 L/D, но для DCIM оно достигает значительных 30.